- Promote maritime freight
- The central issue, order planning
- Medical managers, key players
- The lead time
- The planning tool
- Optimisation of supply times
- Reefer containers
- The "approach" teams
- Direct supply logistics platforms
- Sea transport, much less expensive than air transport
- Success factors
- And now?
The medical aid organisation Médecins Sans Frontières France supplies the health structures it supports mainly from Europe. The supply of medicines and medical consumables, subject to strict regulations, is usually done by air freight, which is a major emitter of greenhouse gases (GHG).
Promote maritime freight
Médecins Sans Frontières France has been working for the past ten years to reduce the volume of goods transported by air and systematically favors maritime transport, which emits much less GHG. In 2021, 67% of the goods transported by the organisation was carried by sea and only 29% by air, whereas air transport represented 70% of the volume transported in the 2010s.
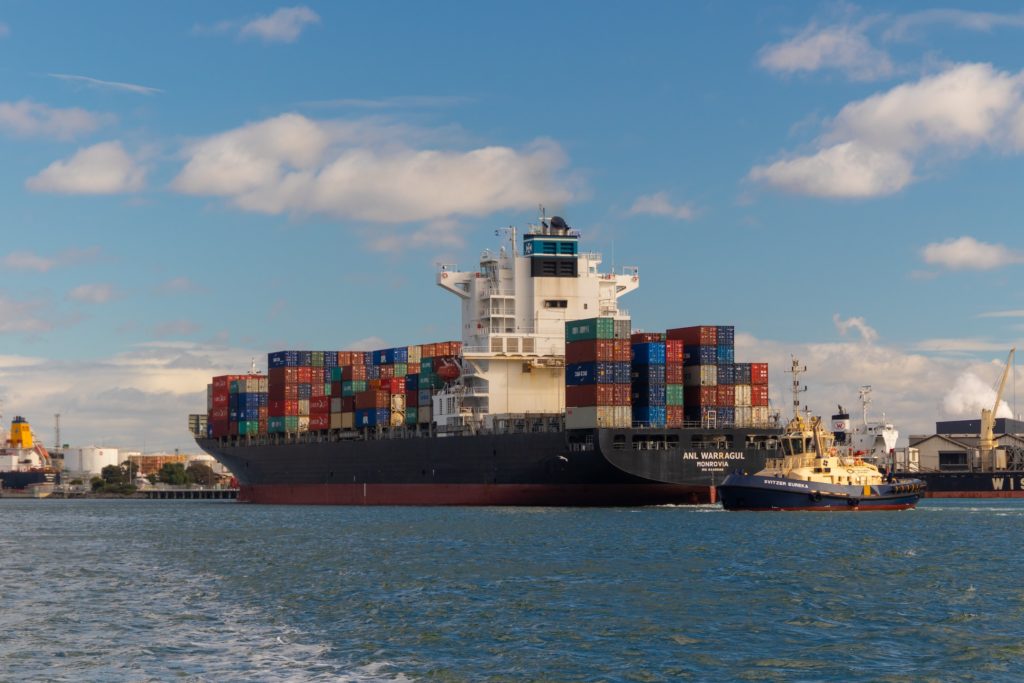
The central issue, order planning
This change is the result of a reflection carried out in collaboration with the medical managers on the entire supply chain of the organisation. The planning of medical orders, carried out in the different health structures supported by MSF France, was identified as the main lever of change. Previously, many “urgent” orders, sent by air, were destined for regular projects and not for emergency projects. They were most often intended to compensate for stock-outs which could be anticipated and avoided through good planning.
Medical managers, key players
The order is initially prepared by the medical field managers who consider parameters such as consumption, existing stock, buffer stock and lead time. The preparation work done by the medical managers is essential and complex because the orders can include many items, some of which are perishable or dangerous or require strict compliance with the cold chain. After being prepared by the medical team, the order is formalised by the logistics team. It is then validated by the country coordination team and confirmed by the head office managers. The validation steps are facilitated by the computerised order management tool called “the portal”. The next steps are carried out by MSF France’s central purchasing office, “MSF Logistique” located in Bordeaux, which collects the items, packs them and organises the transport. The order is then received in the field.
The lead time
Discussions with the medical managers quickly revealed that there were misunderstandings about one key point – the lead time. Lead time is the time between the beginning of the ordering process and the delivery of the goods. Misunderstood, the lead time was badly indicated in the documents, most often minimised, generating bad planning, orders in insufficient quantities and thus stock shortages. Airfreight had to be organised to supply the health facilities as quickly as possible. Since 2016, medical and logistics managers have been meeting regularly during training sessions to ensure a common understanding of the supply chain and of the notion of lead time.
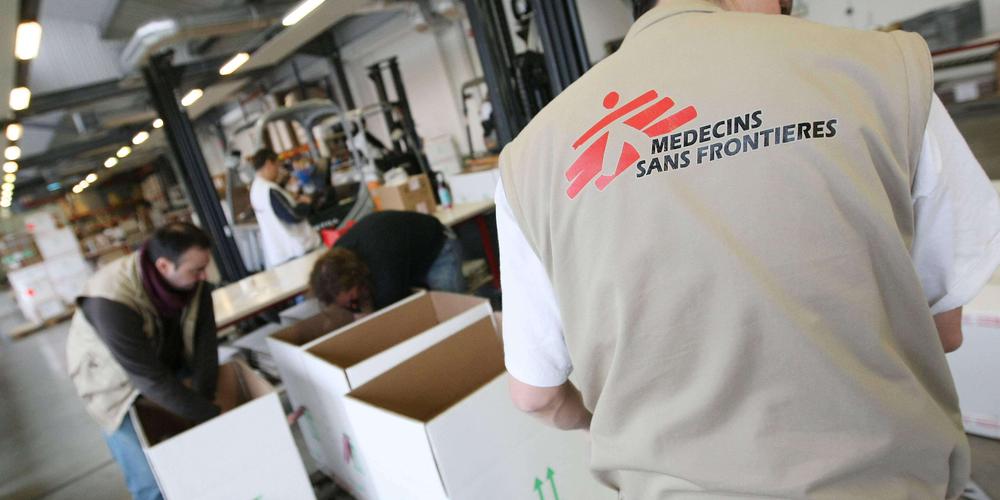
The planning tool
To better plan orders and avoid the need for air transport, MSF France has developed a tool, in the form of “Lead Time Performance” sheets, in which the procurement process is broken down into 10 key steps. Each period between the steps forms a part of the lead time. The duration of each segment of this lead time is precisely recorded for each country and regularly updated. With a good knowledge of the duration of each of these steps, it is easy to calculate the total lead time accurately. If the time needed to prepare and deliver the order is well known, it is then possible to adjust the quantities according to this time and to supply enough to avoid stock-outs in the field. This also allows for a longer transport time to be included, thus facilitating sea freight.
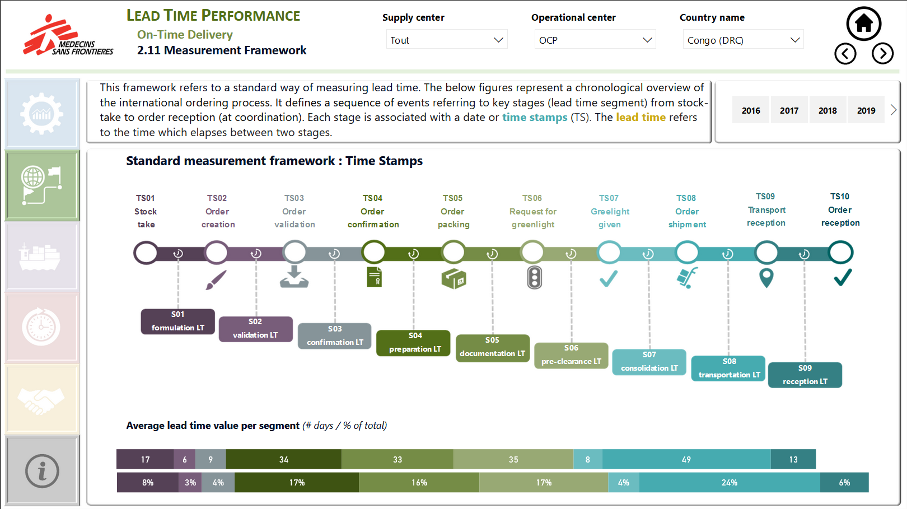
Optimisation of supply times
Knowing each key step and its duration helps optimise and possibly overlap certain tasks, thus reducing the total time. For example, tax exemption and pre-clearance formalities are performed during transport and completed once the ship arrives at its destination. In the case of air freight, the entire pre-clearance procedure is done before departure, so that the goods can be received and, most importantly, stored correctly when the plane arrives. This can greatly reduce the difference in time between sea and air transport. In some cases where the procedures are particularly long, sometimes up to eight weeks, sea transport is competitive.
A big part of our work was to deconstruct the belief among medical officials that the boat was taking too long. Caroline Blondel, MSF France supply manager
Reefer containers
The transport of medicines and medical products by sea freight is only possible thanks to the so-called “Reefer” refrigerated containers, which have been studied and tested by MSF for the past ten years. Reefer containers, equipped with a refrigeration unit connected to the ship’s power supply, maintain a controlled temperature during the entire transport. Common medicines are thus maintained at a temperature between 15°C and 25°C, which guarantees the quality of the products. MSF France is currently studying the possibility of transporting medicines that must be kept between 2°C and 8°C by sea.
The "approach" teams
Since the 2010s, the supply sector has developed significantly within the organisation and a service specifically dedicated to “supply” has been created within the “Logistics” department. Many specialised positions have been created in the capitals and in the projects.
Supply managers, as well as import and transport managers, have joined the teams in the countries where there is the most activity. Dedicated supply positions, supply officers and inventory managers, have also strengthened the teams in most of the countries.
Direct supply logistics platforms
The logistics platforms in Dubai, created by MSF Logistique, and in Kampala and Nairobi, created respectively by MSF Switzerland and MSF Supply (the central purchasing office of MSF Belgium), allow the organisation to supply neighbouring missions while minimising air transport. The platforms are supplied directly by the suppliers and the goods do not go through the European purchasing centre. Transport is thus significantly reduced, especially when suppliers are located in Asia. The Dubai platform has made it possible to reduce air transport to Afghanistan and to use road transport to Yemen.
Sea transport, much less expensive than air transport
This change of transport mode is of course facilitated by the financial savings made, as sea transport is much less expensive than air transport. Transporting a ton of goods by sea freight costs an average of € 250, while the same ton transported by air freight costs an average of € 5,300.
Success factors
The success of this change is due to a detailed analysis of the existing order process in collaboration with the various actors involved, including the medical and logistics teams.
A more detailed study of the international ordering process and the different steps that make up the lead time, by country, by geographical area or by type of product, has made it possible to establish precise timeframes and to optimise the entire supply chain.
Orders are continuously analysed to identify urgent orders for emergency projects that require air freight. Shipments by boat are preferred for regular projects.
Training sessions for medical managers, pharmacists and supply logisticians have helped them gain a common understanding of the various issues related to supply, as well as possible improvements and developments in the field.
And now?
According to MSF France supply managers, it would be possible to further reduce the proportion of air transport. Medicines that need to be kept in a cold chain could be transported in refrigerated sea containers with a constant interior temperature of between 2° and 8°. The sensors called “Log Tags”, placed inside the containers, regularly record the temperature and humidity, thus making it possible to verify if the cold chain has been interrupted during transport.
The proportion of procurement that is done directly by suppliers without going through the European central purchasing office could be increased. It would also be possible to increase domestic road transport in certain countries that currently systematically use air transport. The development of new regional hubs would increase both “direct supplier” sourcing and road transport as an alternative to air. Local or regional sourcing opportunities for items such as therapeutic foods, personal protective equipment, or certain medical consumables are also being explored.
Better planning of medical orders, combined with the use of refrigerated containers, the increase in supply teams or the installation of regional logistics platforms, have made it possible to significantly reduce air freight in favour of sea freight. A reduction of 41% in the proportion of air transport over the last 10 years has enabled a direct reduction in the organisations’s GHG emissions. This proportion may fall further to 25% in the coming years.
MSF Logistique
Photo credit
Cover photo © Rafael de Campos/Pexels.